Discover What is Porosity in Welding and Its Effect on Architectural Stability
Discover What is Porosity in Welding and Its Effect on Architectural Stability
Blog Article
Unraveling the Secret of Porosity in Welding: Tips for Minimizing Flaws and Making The Most Of Quality
In the intricate globe of welding, porosity continues to be a consistent obstacle that can dramatically influence the high quality and stability of bonded joints. As we dive into the midsts of porosity in welding, revealing the keys to its avoidance and control will certainly be extremely important for professionals seeking to master the art of premium weldments.
Understanding Porosity in Welding
Porosity in welding, an usual issue experienced by welders, describes the existence of gas pockets or spaces in the welded product, which can jeopardize the honesty and high quality of the weld. These gas pockets are usually trapped throughout the welding procedure as a result of various factors such as inappropriate shielding gas, contaminated base materials, or inaccurate welding criteria. The formation of porosity can deteriorate the weld, making it susceptible to cracking and corrosion, eventually causing structural failings.
By acknowledging the relevance of preserving appropriate gas securing, ensuring the cleanliness of base materials, and optimizing welding setups, welders can considerably decrease the likelihood of porosity formation. In general, a detailed understanding of porosity in welding is crucial for welders to create high-grade and resilient welds.

Typical Root Causes Of Porosity
When evaluating welding procedures for potential high quality problems, understanding the usual reasons of porosity is important for keeping weld integrity and protecting against structural failures. Porosity, defined by the presence of dental caries or gaps in the weld metal, can dramatically jeopardize the mechanical residential properties of a bonded joint.
Furthermore, welding at incorrect specifications, such as excessively high travel speeds or currents, can produce excessive turbulence in the weld swimming pool, trapping gases and creating porosity. By resolving these typical causes with appropriate gas securing, material prep work, and adherence to optimum welding parameters, welders can decrease porosity and enhance the high quality of their welds.
Methods for Porosity Avoidance
Executing effective safety nets is crucial in reducing the occurrence of porosity in welding procedures. One method for porosity prevention is making sure appropriate cleaning of the base metal before welding. Impurities such as oil, grease, corrosion, and paint can cause porosity, so extensive cleaning making use of suitable solvents or mechanical approaches is crucial.

An additional trick safety net is the choice of the appropriate welding consumables. Making use of top notch filler materials and protecting gases that appropriate for the base steel and welding procedure can considerably lower the risk of porosity. Additionally, maintaining proper welding criteria, such as voltage, existing, travel speed, and gas flow rate, is important for porosity avoidance. Differing the suggested settings can cause inappropriate gas insurance coverage and poor combination, causing porosity.
Furthermore, using appropriate welding methods, such as maintaining a consistent traveling rate, electrode angle, and arc length, can assist avoid porosity (What is Porosity). Adequate training of welders to guarantee they adhere to finest practices and quality control procedures is resource likewise crucial in minimizing porosity flaws in welding
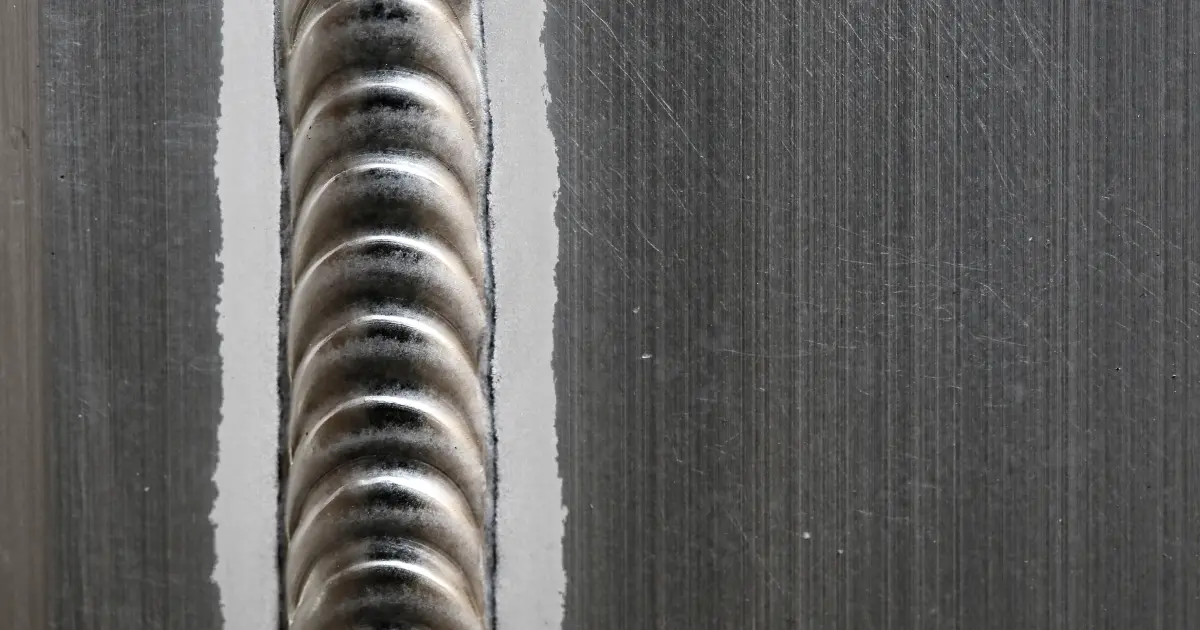
Finest Practices for Top Quality Welds
Ensuring adherence to sector criteria and correct weld joint preparation are basic elements of accomplishing constantly high-grade welds. In enhancement to these foundational steps, there are a number of best practices that welders can implement to additionally improve the quality of their welds. One key method is preserving appropriate sanitation in the welding area. Impurities such as oil, oil, rust, and paint can negatively impact the high quality of the weld, resulting in flaws. Completely cleaning up the workpiece and bordering location prior to welding can aid minimize these issues.
One more best method is to meticulously pick the suitable welding parameters for the details materials being signed up with. Appropriate parameter option guarantees ideal weld penetration, combination, and overall quality. Utilizing premium welding consumables, such as electrodes and filler metals, can substantially impact the final weld high quality.
Importance of Porosity Control
Porosity control plays a critical function in making certain the honesty and high quality of welding joints. Porosity, characterized by the existence of tooth cavities or spaces within the weld metal, can significantly jeopardize the mechanical homes and YOURURL.com architectural stability of the weld. Too much porosity weakens the weld, making it much more vulnerable to breaking, corrosion, and total failure under operational tons.
Reliable porosity control is crucial for maintaining the wanted go to this site mechanical residential properties, such as strength, ductility, and durability, of the welded joint. What is Porosity. By minimizing porosity, welders can enhance the general top quality and reliability of the weld, guaranteeing that it fulfills the efficiency needs of the desired application
Furthermore, porosity control is vital for achieving the wanted aesthetic look of the weld. Too much porosity not only damages the weld however likewise detracts from its visual appeal, which can be critical in industries where visual appeals are very important. Proper porosity control methods, such as utilizing the correct shielding gas, regulating the welding criteria, and making certain correct tidiness of the base products, are essential for producing top quality welds with minimal problems.
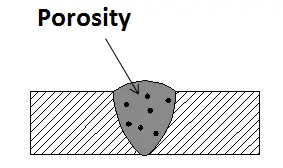
Final Thought
In conclusion, porosity in welding is an usual problem that can endanger the quality of the weld. It is vital to regulate porosity in welding to make certain the honesty and stamina of the final item.
Report this page